We want to help you
Please leave your contact details. We will get back to you as soon as possible!
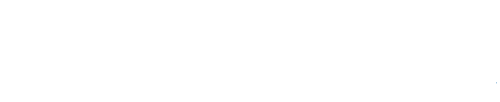
Ultrasonic welding consists of a process ofย mechanical vibration at ultrasonic frequency where the contact zone between the sonotrode and the part to be welded undergoes a merger at the local level.
The 50/60Hz mains frequency is transformed and amplified by the ultrasound generator in the form of electrical signal and converted by the piezoelectric transducer into energy of movement.
This energy supplied by the generator and applied to the acoustic assembly must be sufficient to overcome the inertial moments of the masses to be set in motion and the friction between the parts.
The advantages of advanced technology such as ultrasonic welding are numerous:
Ultrasonic welding is one of the safest, most effective and fastest methods of joining thermoplastic materials.
The welding time is around milliseconds and it is possible to weld moulded parts and thermoplastic fabrics.
The ultrasonic technology allows the cutting and simultaneous closing of the synthetic fibres of fabrics, avoiding the typical fraying effect. During and after the cutting operation, the tool remains clean at all times, and the use of ultrasound is safe for operators as it does not burn and does not produce toxic fumes.
Ultrasonic stitching makes it possible to join two or more layers of fabric without adding adhesives, solvents or mechanical fixings. In addition, ultrasonic seams are hermetically sealed, preserving the contents of the product. One of the advantages is certainly related to energy, as the welding process has no negative impact.
Ultrasonic riveting is used to melt a peg, or pin, introduced into a hole. The plastic pin is brought into contact with the sonotrode, melting and forming a crimping head. This technique can also be used to fasten different materials or metal parts, such as car, motorhome and boat parts, or special electrical components (plugs, sockets, multi-sockets, connectors), or air filters and petrol/diesel filters.
This operation stems from the need to incorporate brass rivets into a thermoplastic material. The hole in the plastic melts under the action of ultrasound, allowing the rivet to be inserted. The rivet has a knurl, which increases the adhesion of the solder. Once the welded plastic has solidified, the rivet is perfectly incorporated.
In order to reduce the areas of friction between the parts, which make it difficult to initiate the melting process, it is advisable to create geometric protuberances on the parts themselves, known as energy directors, which allow the material to be melted over a relatively small area.
In order to choose the most suitable energy director geometry for your application, we list some examples below and in any case we are available to offer our experience and technical knowledge.
Common joints that incorporate the use of an energy director include: butt joints, segmented joints and tongue and groove joints.
Please leave your contact details. We will get back to you as soon as possible!